Provided contractual engineering consultancy to the following projects:
• Flow Assurance Support - Husky Energy, West White Rose Project.
• Process Engineering Consultant - IMV Projects Atlantic Inc. - Flow Assurance, pipeline hydraulics, surface facilities, and natural gas plant troubleshooting and optimization for multiple projects.
- Feasibility studies of Labrador gas development – Gas and gas condensate production systems, Flow Assurance of subsea production systems and gas transport pipelines, gas processing facilities including slug catcher, inlet separators, condensate stabilization and gas dehydration and dew point control, MEG injection and hydrate management for production of 500 MMSCFD of gas from the offshore gas condensate reservoir
- Simulation and hydraulics analysis, gas compression and line heating systems for 300, 500, 1200 km gas transport pipelines for Shell Canada
- Prepared technical proposal for Petrobangla supervision of construction, testing, commissioning & acceptance of 110 MT per-day capacity NGL Fractionation Plant at Kailashtilla , Bangladesh
• Project Manager, Process Engineering Lead, and Senior Engineering Consultant - Centre for Marine Compressed Natural Gas (CMCNG) Inc.
- Participated in HAZID and HAZOPs and design activities for the Gas compression and heating and cooling flow loop systems, and high pressure gas storage systems
- Managed the set up and procurement of high pressure gas PVT reservoir fluids systems –provided consultancy to commercialize the lab (the 1st in Atlantic and West of Alberta in Canada) now operating under commercial corporate name of Petroforma
- Led a number of studies related to the impact of cold jet on high pressure vessels and surrounding piping and facilities using CFD method
- Supervised commercial industry JIP on dynamic modelling of loading and unloading systems involving high pressure gas tests, and modelling hydrate formation under near liquid free flow conditions and published several papers and presentation in journals and international conferences
• Consultant - National Iranian Gas Co. (NIGC), South Pars Gas Processing Facilities, South Pars area and Tehran, Iran - resolved operational problems, provided technical training programs, supervised progress of several projects related to optimization of LNG processes and nitrogen rejection.
- Providing expert consultation on gas plant operations and troubleshooting including:
- MDEA contamination with MEG, chlorine and calcium
- Foaming of contactor tower
- Corrosion of 316 stainless steel heat exchanger and pumps impellers
- Provided expert review on the NIGC feasibility studies including following examples:
- Feasibility of using peak shaving LNG facilities for strategic storage of natural gas for winter gas consumption surge
- Feasibility of nitrogen rejection systems to improve quality of the Iranian export gas
- Feasibility of ethane recovery and deep-cut NGL units for existing gas processing facilities
- NGL recovery using membrane technology
- Holding workshops for training of plant operations engineering staff on following areas:
- Design and Operations of Gas Handling Facilities
- Design and Operations of Gas Sweetening Systems
- Design and Operations of Dew Pointing and Gas Liquids Refrigeration Systems
- Reviewed design documentation, and participated in the construction and installation supervision of a demonstration unit of Sulfiran H2S removal and conversion process on the amine tail gas system (100MMSCFD) of the Fajr Jam Gas Processing Facilities.The demo unit ($100 million) was constructed, installed, commissioned and tested at the plant in Fars Province, Iran
- Sulphur induced degradation of amine solution in the Hasheminejad (Khangiran) gas processing plant (2,000MMSCFD plant), including test of solvent, determining the root cause of problem advised potential solutions
- Coke formation on silica gel and molecular sieve beds of the NGL recovery and dew point control unit of Khangiran gas plant, including diagnoses of the problem and advising on potential mitigation scenarios
- Amine degradation and corrosion in Fajr-e-Jam (Kanagan) gas processing facilities including diagnosis of the problem and advising on mitigation solutions
- Monitoring the performance of amine solutions for the Fajr-e-Jam (Kangan) and Hasheminejad (Khangiran) facilities: including analysis of amine solutions for active amine, degradation products, heat stable salts, total dissolved solids, total suspended solid, foaming characteristics
- Reviewed performance of activated carbon and particle filters of the Fajr-e-Jam (Kangan) gas facilities including analysis of activated carbon, review of carbon manufacturer recommended change-out periods, developing regeneration systems
- Amine degradation and corrosion at the amine stripping tower and reboiler in the gas sweetening unit of Bandar-e-Imam (Mahshahr) Petrochemical Facilities including sampling and analysis of solvent, review of stripper column and reboiler design, recommended step-by-step design modifications and developed solvent monitoring procedures for the plant
- Developed process and led FEED for the recovery of propane and butanes from flare gases at the Abadan petroleum refinery to feed ethylene plant at the Abadan petrochemical facilities, including process simulation of the process, design of process systems and costing the facility
- Study of replacing DEA with DEA-MDEA mixed solvent including solubility tests, absorption capacity of the mix in test facilities, HYSYS process simulation and benchmarking against test results, developing thermodynamic models and tuning the models to improve simulator predictions
- Participated in the development high efficiency MDEA based solvents – CO2 and H2S and mercaptans and other sulphur components solubility tests, absorption efficiency tests in gas contactor unit
- Developed amine/glycol reclaiming systems based on vacuum distillation process including process modelling and simulation, design and construction of pilot and demonstration plants, equipment procurement and contractors management
- Developed process to capture mercaptans from NGLs and used them as odorant.Managed technology transfer programs in partnership with Russians technology owners
- Developed Sulfiran (Iron Redox H2S Conversion)process including solution formulations, bench scale tests, design of pilot plants, construction and installation of pilot plant in the sulphur plant (SRU) of the Tehran refinery, developed design procedures, developed colloidal sulphur separation systems, long-term test programs and proving concepts, patenting the technology and participated in the construction of demonstration plant in Kangan gas processing plant
- Developed carbon molecular sieve for gas separation (N2 from natural gas, oxygen from air, etc.) including developing carbon synthesis procedures and equipment, isotherm set-ups, characterization systems including advanced microscopy, pore size characterization, raw material characterization as well as design of industrial scale furnaces to produce at large scale
• Process Consultant - Taravosh Jam and FAP Co. (PJS), Tehran, Iran - Consulted on natural gas, oil, and petrochemical process design/simulation projects including dehydration, NGL recovery, surface facilities, natural gas sweetening, line heater and sea water deaerator design and construction.
- Basic Engineering, construction and procurement supervision (equipment and service company coordination) of three sea water vacuum deaeration systems including deaerator towers, seal water vacuum pumps, ejectors, instrumentations, developing operating manuals, commissioning and troubleshooting, and test methods for Sirri Island Projects D and C,Yadavaran Oil Fields and, Reshadat Projects, client: South Pars Natural Gas Developments and Iran Marine Industrial Co, Sadra, Oil and Gas Division,
- Basic Engineering and construction and procurement supervision for amine gas sweetening pilot plant (capacity of 4 gpm) for the National Iranian Oil company including process simulation and modelling, material and energy balance, piping and process equipment design, developing equipment datasheets, HAZOP analysis
- Process simulation and design for processing plant for improving gas liquids recovery for Kangan (Fajr Jam) processing facilities recovering liquids from de-ethanizer and condensate stabilisation system, 110 MSm3/d (4 Billion CFD) facility including 8 trains
- Led the Pre-FEED activities for deep-cut NGL recovery - Enhancement of NGL, LPG, and ethane production in potential Iranian gas processing facilities for National Iranian Gas Company (NIGC)
- Led troubleshooting of vacuum batch distillation reclaiming system for the recovery of diethanolamine from spent solutions, Shizar Chimie, Isfahan, Iran
- Prepared technical proposal for 55,000 bbl/d crude desalter packages for Marun, Gachsaran and Labeh Sefid production facilities including design and construction of electrostatic deslaters, crude and dilution water heaters and piping and control systems.
- Prepared technical proposal for Ahwaz Oil Company methane stripping deaerator system
- Performed preliminary basic engineering and prepared equipment specifications for first round proposal for an MDEA-MEG reclaiming plant based on vacuum distillation with a capacity of 24 m3/d for National Iranian Gas Company – South Pars Phases 1 and 2 Facilities, Assaluyeh, Iran
- Performed preliminary basic engineering and process design review of condensate dewatering separators, free water knock out (FWKO) drums and test separators for Phases 17 and 18 for South Pars Offshore facilities including selection and specifying of internals, Assaluyeh, Iran; prepared technical proposal
• Scientific and Technical Consultant - National Iranian Oil Co. (NIOC), Research Institute of Petroleum Industry, Tehran, Iran - Consulted on design and construction of natural gas processing pilot plants; and oversaw progress of projects.
- Engineering Lead of feasibility and pre-FFED for NIOC Gas-to-Liquids (GTL) project in partnership with Statoil and PetroSA including offshore field development, onshore gas receiving and processing facilities, GTL plant including air separation facilities, Fischer-Tropsch conversion, synthetic liquids upgrading with a capacity of 60,000 bpd (diesel, LPG, Kerosene, and naphtha liquid products), and site selection
- Engineering Lead of the Pre-FEED and FEED stages of constructing a 100 bbl/d GTL demo unit at Shiraz petrochemical facility taking feed from methanol plant gas reformer included site visits, locating optimum location, HAZOP reviews, PFD and P&ID reviews, selection and qualification of contractors and unit fabrication companies
- Project manager of gas-to-liquids technology development program for NIOC including catalyst development programs, pilot plant design and constructing for gas reforming and gas conversion systems, technology transfer program involving international partners (Statoil and Lurgi)
|
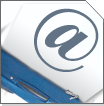 |